Mercedes-Benz takes a major step towards sustainability with new battery recycling plant
Mercedes-Benz has just opened a groundbreaking battery recycling facility in Kuppenheim, Germany, marking a huge leap forward in sustainable electric vehicle (EV) production.
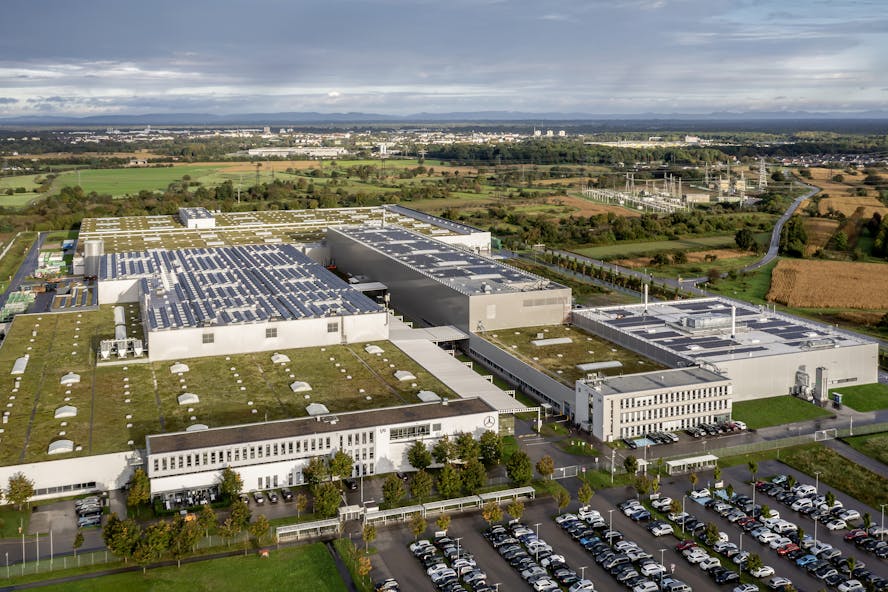
The factory, the first of its kind in Europe, features an innovative mechanical-hydrometallurgical process that allows the recovery of more than 96% of valuable materials from used EV batteries. This is a significant milestone in the company’s ambitious goal to reduce reliance on raw resources, minimize waste, and promote a true circular economy.
What is Hydrometallurgy?
-
Hydrometallurgy is a process that recovers or recycles metals from ores and waste materials using water-based solutions
-
This process works at lower temperatures compared to other methods of extraction
A game-changing facility for the future of EVs
This new recycling plant isn't just another factory—it represents a transformative approach to battery lifecycle management. By recovering scarce materials like lithium, nickel, and cobalt, Mercedes is taking ownership of the full battery supply chain. The recycled materials can be used to produce over 50,000 new battery modules annually, helping to meet the growing demand for electric vehicles while cutting down on the need for new raw materials.
What’s even more impressive is that the plant operates in a net carbon-neutral manner, powered entirely by renewable energy. Mercedes-Benz has invested heavily in the facility, underlining its commitment to a future where sustainability and value creation go hand in hand.
Design for circularity
In collaboration with technology partner Primobius, Mercedes-Benz is demonstrating that the future of the auto industry is not just electric, but circular.
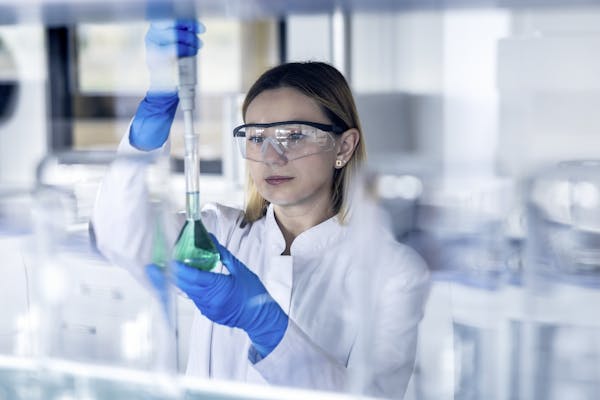
Traditional battery recycling processes are energy-intensive and wasteful, but this new hydrometallurgical approach is far more efficient, using less energy and recovering materials with greater purity. This allows Mercedes-Benz to reclaim essential battery components while significantly reducing the environmental impact of manufacturing.
The plant is part of a broader push by Mercedes-Benz to lead the way in sustainable mobility. The company’s "Design for Circularity" approach focuses on the entire battery lifecycle, from initial design through to reconditioning and recycling. This long-term vision ensures that Mercedes-Benz vehicles are as eco-friendly as possible, both on the road and once their batteries reach the end of their life.
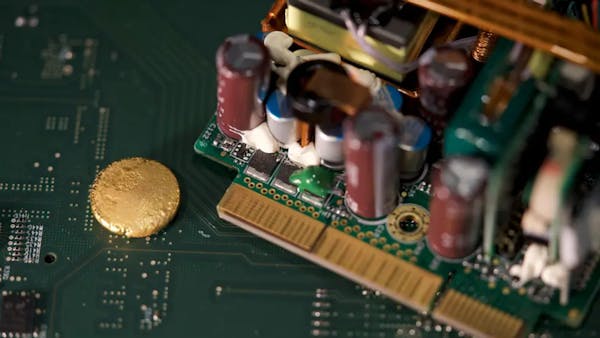
Other companies are also recognising the potential value in tech waste. The Royal Mint, for example, has begun extracting gold from discarded electronic waste, or e-waste, which includes old phones, computers, and TVs. At their new facility in Wales, the Mint uses an innovative process to recover gold from circuit boards. This approach, known as "urban mining," allows them to repurpose a finite resource from tech waste into valuable products like jewellery and coins. The initiative reflects a broader trend of businesses finding ways to create value from waste, further showcasing how recycling can be both sustainable and profitable.
Germany: a hub for green automotive innovation
Germany, already known as a leader in automotive engineering, is cementing its role as a centre for green innovation.
The knowledge gained from the Kuppenheim plant isn’t just a win for Mercedes; it’s a win for the entire EV industry, and could help scale up battery recycling efforts across Europe, making the entire EV market more sustainable.
As Germany's Federal Chancellor Olaf Scholz pointed out at the plant’s opening, this facility is a crucial step in achieving climate targets and ensuring that Germany remains a global leader in cutting-edge technology. Mercedes-Benz has proven that investing in sustainability can go hand in hand with profitability.
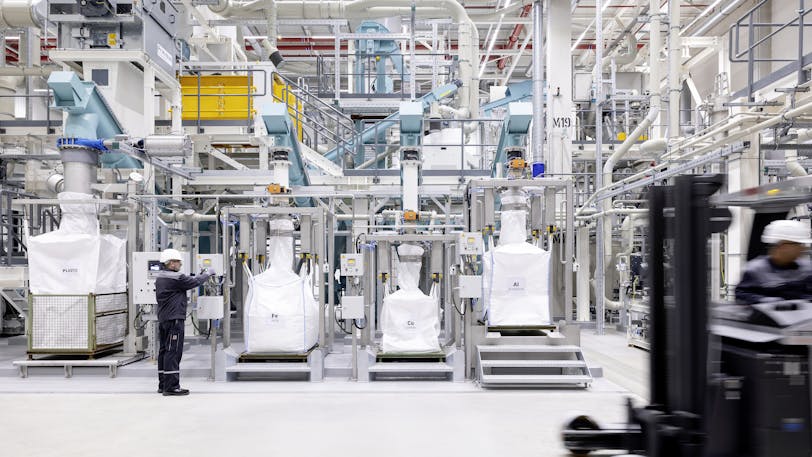
The future of the automobile is electric, and batteries are an essential component of this. To produce batteries in a resource-conserving and sustainable way, recycling is also key. The circular economy is a growth engine and, at the same time, an essential building block for achieving our climate targets!
The road ahead
At DriveElectric, we provide electric vehicle lease options to our customers and the sustainability of the vehicles we love and lease is a major factor of concern for both our customers and the planet. We are a Planetmark certified business and are working to reduce our own carbon emissions so it's uplifting to read about a big project like this that will have a lasting and far reaching environmental impact.
Mercedes' investment in battery recycling means that the lifecycle of an EV is becoming more eco-friendly with every innovation. As the EV market grows, this kind of circular approach will become the new standard. Yes please. It's a future we can all look forward to.
To learn more about EVs and emissions read our How clean are electric cars? guide
Our expert guides
6 surprising things you didn’t know about electric vans
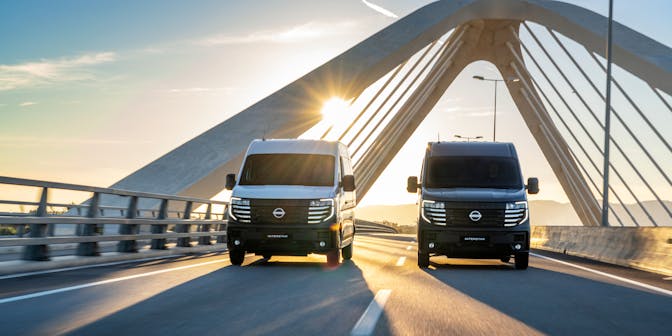
Understanding Vehicle Excise Duty (VED) or "Road Tax" for EVs
How to save money on a new car with Salary Sacrifice
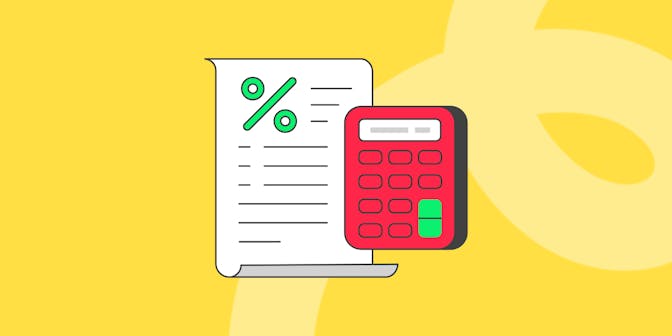